Welding related
Detect, identify
metal type - see metals
Filler metal
ER309L - good maintenance filler - works well with combination
metals - like carbon steel to stainless. Best bet for mystery metals
TIG electrode
notes
Tungsten Diameter |
tungsten area |
Gas Cup (Inside Dia.) |
Typical Current Range (Amps) |
|
Direct Current, DC |
Alternating Current
AC
|
DCEN |
70% Penetration |
(50/50) Balanced Wave AC |
Ceriated
Thoriated
Lanthanated
|
Zirconiated
|
Ceriated
Thoriated
Lanthanated
|
Zirconiated
|
Ceriated
Thoriated
Lanthanated
|
.040 |
Tables
63 |
#5 (3/8 in) |
15–80 |
20–60 |
15–80 |
10–30 |
20–60 |
.062 (1/16 in) |
97
|
#5 (3/8 in) |
70–150 |
50–100 |
70–150 |
30–80 |
60–120 |
.093 (3/32 in) |
146
|
#8 (1/2 in) |
150–250 |
100–160 |
140–235 |
60–130 |
100–180 |
.125 (1/8 in) |
196
|
#8 (1/2 in) |
250–400 |
150–200 |
225–325 |
100–180 |
160–250 |
DCEN = Direct Current Electrode Negative (Straight
Polarity).
all values are based on the use of argon as a shielding gas.
other current may be employed depending gas, type equipment,
and application.
|
Lanthanated is probably the best all around type.
Color codes
Type of Tungsten
|
Color code
|
Description
|
Pure
|
Green
|
Provides good arc stability for AC welding.
Reasonably good resistance to contamination. Lowest current
carrying capacity.
Least expensive. Maintains a balled end.
|
Ceriated
CeO2
1.8% to 2.2%
|
Gray
|
Similar performance to thoriated tungsten.
Easy arc starting, good arc stability, long life. Possible
replacement for thoriated.
|
Thoriated
ThO2
1.7% to 2.2%
|
Red
Yellow
|
Easier arc starting. Higher current capacity.
Greater arc stability. High resistance to weld pool
contamination.
Difficult to maintain balled end on AC.
|
Lanthanated
La2O3
1.3% to 1.7%
|
Gold
Black
Blue
Yellow
|
Similar performance to thoriated tungsten.
Easy arc starting, good arc stability, long life, high
current capacity.
Possible replacement for thoriated.
|
Zirconiated
ZrO2
0.15% to 0.40%
|
Brown
|
Excellent for AC welding due to favorable
retention of balled end, high resistance to contamination,
and
good arc starting. Preferred when tungsten contamination of
weld is intolerable.
|
Tungsten Pure Green
Tig on cast iron - use Nickle 99 - actually a type of brazing.
Tip stick out rule of thumb - should be about the same as the cup
opening.
Filler for Au casting - 4047
Clamping and weld
distortion
Despite what people say - it is best to only clamp until the weld
tacks are in place. This is the same reason restraining the part (by
being fast so the rest of the metal restrains - or clamping)
increases the bend amount in flame straightening.
Argon Gas flow
Good starting point - set the LPM to the cup size.
Tool steel like rod
-
weld mold 958
D2 tig filler metal
Stellite 6/12 tig filler - very hard https://www.stellite.com/us/en/products/hardfacing-alloys/welding-rod.html
c83 rod
Spot Welding
Electrode tips copper tungsten or copper chrome
Spot welding aluminum
Put the aluminum sheets in between sacrificial stainless sheets.
Silver solder
Stay bright - low temp
High temp use Safety silv 56
Stay-Silv by Harris (Robrenz uses) high temp brazing flux(water
based) turns clear at temp
Heat bigger part first
Harris Safety-Silv 45 brazing temperature is1370⁰ to 1550⁰ F.
Safety-Silv 56 is 1200⁰ to 1400⁰ F.
Safety Silv white flux active range 1000⁰ to 1600⁰ F. Safety Silv
black flux active range 1050⁰ to 1700⁰ F. Also the black flux
has a boron content that extends its working time. Flux activity is
time limited at brazing temperature.
The liquid flux oxidizes in air over time forming a tough film that
inhibits joint wetting. For that reason, plan your operation - do
not dally.
A final point is joint cleanliness. Clean the joint thoroughly, then
scrub the joint surfaces with Comet cleanser, a stiff brush, and
water followed by a hot water rinse. Do not follow with a solvent
clean (any solvent) Conventional wisdom decrees a final
acetone wash. Acetone is a commercial product containing impurities,
reaction fractions, wax, and tramp particulates. These pyrolyze and
inhibit flux activity and joint wetting.
Comet cleanser as your last step makes a huge difference
ZYP Coatings makes a Boron Nitride Aerosol Lubricoat that can be
used as a solder resist. Cheaper to get Boron Nitride as 'white
graphite'.. - found powder - mix with bit of solvent (acetone
or ethanol) Spread on as a resist.
mystery metal -
pot - aluminum?
AC - 200A Pulse - 120/s PK95 Bk70 240Hz - fresh air..
TIG Brazing -
silicone bronze
Don't puddle base metal -Stay over bronze - just hot enough
to not ball up. AC or DC - lay-wire- don't dab - pulse
DC is probably best -- 100A good place to start.. clean everything
- even rod .. Pulsing 1-2/sec 33%-background 33% at
peak lets you lay-wire - dabbing makes oxides. Half
strength of steel - but less distortion.
Tig Brazing Cast
Iron
For cast iron - preheat to 425C
Si Bronze AWS A 5.27 RBCuZn-C melts at 860-890C Tensile Strength 460
MPa 60-68kpsu
Nickel 99 NICKEL 99 AWS/SFA 5.15 Eni-Cl melts at 1453C
Yield - 36-50ksi
TIG settings
starting recipes
Aluminum
Frequency - 90-120 - the higher the frequency the tighter the
arc-cone - and less heat/penetration
Balance -- about 70 Lower cleans more
Pulse settings (helps with melt through) 1.2-2hz (Pulses-per-Second)
for adding filler synchronized. On time 50% Back ground 25-40%
Metal Files
Cut numbers are not the same for different types of files! They
really should specify the Pitch - but don't! Need a Graticule
or Reticle to measure it.
Cut rating of files:
Cut number
|
Pitch um
Needle
and Escapement
|
Pitch um
Swiss pattern
4"-8"
|
00
|
498
|
620
|
0
|
397 |
498
|
1
|
322
|
397
|
2
|
261
|
322
|
4
|
179
|
217
|
5
|
147
|
|
6
|
119
|
147
|
8
|
86
|
|
Adhesives
epoxy
Frisket film makes for a good resist.
Loctite
Red loctite 263
mounting wax
https://www.amazon.de/WEKEM-Sekundenkleber-hochviskos-dickfl%C3%BCssig-schwarz/dp/B01AWFQBV
WEKEM WK-2400 Good for gluing shim stock for stops
MEK can be used to thin epoxy..
Loctite 1712314 repositional spray adhesive
Hylomar
- gasket material - also keeps things from vibrating lose that get
taken apart repeatably - not as strong as loctite blue. Does
not significantly change dry fit up dimentions. Requires true
surfaces.
Loctite colors.
Purple Low Strength Threadlockers.
Blue (243): Medium Strength Threadlockers.
Green (294): Penetrating Threadlockers. - wicks into cracks - heat
to remove
Red - highest strength -heat to remove.
Black - toughened superglue - 438 for work holding.
styrene butadiene
(Goop) (oil resistant)
Can be smoothed/formed by thinning with Toluene
Chemicals
that have little or no effect on Goop II max
(percentages are given by weight unless otherwise noted.)
Acetic acid (5% and 10%)
Ammonium hydroxide (3.4%)
Ammonium nitrate (50%)
Antifreeze
Beer (3.2% alcohol by volume)
Boric acid (3.1%)
Distilled water
Hydraulic oil
Lactic acid (3.8%)
Milk (fresh, tested at 40 °F)
Motor oil (30w)
Nitric acid (10% and 20%)
Oxalic acid (3.1%)
Phosphoric acid (30% and 60% as P2O5)
Potassium hydroxide (3.4%)
Sodium carbonates (2.7%)
Sodium chloride (10%)
Sulfuric acid (3% and 10%)
Wine (20% alcohol by volume)
exhibits excellent resistance to water, dilute acids and dilute
bases. Thin films of AMAZING GOOP® II MAXTM were immersed in various
chemicals for two weeks and exhibited weight gains of less
than 2% and tensile strength loss of less than 10%. These
chemicals are listed on the left.
Blackmax 380
rubber toughened ethyl cyanoacrylate adhesive with increased
flexibility, peel strength, and enhanced resistance to shock for
temp stops - fixtures
3M-467 tape
adhesive only -- holds things. - replace adhesive on
stickers/plates. - Robrenz recommended.
Teflon tape
mc 76475A51 - lots of varieties - sticky one side - teflon the
other.
Epoxy
PC.7
- good filler and strong - slow set
BSI
Has 5min and the stronger slow set - clear-ish -
Loctite 1373425
Hysol 1C
Top quality epoxy Shore Hardness 65 Shore D, Shear Strength 1500
psi
epoxy tramming -
slide forming
https://www.diamant-polymer.de/en/products/moglice/
https://www.diamant-polymer.de/en/products/dwh/
Rulon 142 or Turcite
DIY moglice - DHW epoxy filled with more than 80% by weight
steel.
-p is paste like
--FL is pourable.
DWH-310-FL viscosity 12k-14K (low viscosity) Steel filled
DWH-310-P low viscosity - coating of parting lines - mounting
surfaces
DWH-311-FL viscosity 20-25k - still low.. aluminum
filled
DWH-314-FL viscosity 28K Mineral filled
Moglice 1000-FL - Has low friction additives
the regular moglice has graphite and molybdenum disulfide -
Recipe from patent - percent by weight:
- epoxy resin: 40-80 --- 60
- molybdenum disulphide: 15-30 22
- graphite: 10-15 12
- aluminum: 5-10 7
- copper: 5-10 7
- alumosilicate: 8-15 (glass )
- polyethylenepolyamine: 5-10. (ph control? likely in most
epoxies )
Poor mans recipe epoxy 70 moly 20 graphite 10 - needs test.
The putty moglice is scrapable - but soft - easy to go to far.
The DWH - fitting epoxy..
Adhesive removal
Plexiglass backing gets old and hard to remove - soak in pure
cleaning ammonia - scrape off the paper layer - let dry - cover with
methanol - wait a bit - scrape.
Bits - drills -
reamers - boring - milling cutters
For hard metal - high Rock
Carbide bur for phenolic SGStool.com 73011 FGR #9 Style A
Diamond burr for aluminum??
O-flutes for plastics https://www.onsrud.com/articles/O-Flutes-For-Mechanical-Plastics.asp
https://www.onsrud.com/Series/SolidCarbide1-2FluteDowncutPlastic.asp
For cutting Sheet
metal - routing
Use chamfered endmill and .1 - .2mm depth of cut, with high feed
rate.
Taps
Always get taps with PM in the part number - powdered metal - HSS
Extensions - best are RITMAR
Lisle LI70500 tap socket set - combine with a
ball spline assembly - ball spline bushings.
Abrasives,
Lapping, and grinding
Lapping Notes
The groves in a lapping plate make a difference. The edge
of what you are lapping will pile up abrasive and cut more - the
groves help prevent this. An iron lapping plate can be
covered with a polycarbonate film (stuck on with some
purple-power) - or use thick aluminum foil (can't find anymore?).
Lapping
details
Lapping Abrasives
PSA diamond film - use PSA only for roughing and be meticulous about
cleanliness, dust or hair will make it almost impossible to use.
With plain film back just spray the back with water and squeegee it
to the plate.
Eye - lap (mcmaster) copper tool for lapping ID to match pins
3M™ Microfinishing Film Roll
12" wide x 25 yard roll of 220 grit Silicon Carbide paper -
Abrasives South Inc. 1-800-255-8112 #18014 roughly $100.00
cerium oxide
At the finest level - lapping after scraping - don't use diamond or
sil-carbide - instead .03um alumina- it breaks down - removable with
kerosine (why not cerium oxide? )
You can see fringes on high spots. Alumina 9Mohs, Cerium oxide 7mohs
- optical rouge lower yet -- iron 4-5 steel knife 5.5 - file 6.5
Graded grits
https://www.hisglassworks.com
https://gotgrit.com/
http://firsthanddiscovery.com/
https://www.us-nano.com/inc/sdetail/21645
https://www.kemet.co.uk
Sand paper for
metal
Most of the skilled people use 3M wet/dry - wet with WD40. - 240 -
320 - 400 followed with Scotch bright is common..
Deburring
Cratex Brightboy stick deburr https://www.cratex.com
Coarse = 125um 1.06um-Ra
Medium = 85um 0.48um-Ra
Fine = 65um 0.30um-Ra
xtra-fine = 25um 0.1um-Ra
Scotch-Brite EXL Unitized Wheel, Silicon Carbide,Fine Grit
Cut off wheel -
use for tool grinding
3M™ Cubitron™ II Cut-Off Wheels for gross material removal (of High
Speed Steel) 1mm thickness 65512
PGS (Precision
Ground Stones)
Clean surface first with solvent - remove oils.
Start off dry - oil on the stone removes the sensitive feel.
Prepare the work by removing large burrs with a file or regular
stone.
Clean and rub the stones first - we want a floating flat feel.
Slide stone gently onto work - you can feel tiny burrs sticking up -
think of these stones as a kind of test tool.
If you feel a big burr - use file or regular stone again.
Feeling something rolling? Stop at once, and clean then rub stones
again.
If things feel smooth try pushing a bit harder - follow grind
direction.
To go a little further - use a bit of acetone or alcohol - don't use
oil. Anhydrous isopropanol likely best. Lubrication removes the
sensitive feel and sound of the stones.
Stones can be cleaned via ultrasonic tank - water based cleaner -
Alconox - allow stones to completely dry before using.
When finished - the bare steel can rust - protect it with your
favorite schmoo.
PGS were invented by Harold E. G. Areneson (RIP) of Professional
Instruments Company - also invented high precision air bearings that
had a central sleeve that apparently compensated for load.
Grinding wheels
Surface grinders normally run at 3-4K-RPM slowing has the
effect of a softer wheel
Typical starting point 46 H or I
10 structure
Percent Concentration Diamond/CBN - concentration is the ratio
between the diamond/CBN grains' weight and the volume of the
abrasive layer. Standard concentration = 100 equals 4.4 carats per
cubic centimeter. Thus concentration can be over 100.. 200
would be 8.8 carats/cm3
Harder J-K 60-80 are for 'form' grinding
Depth of cut 5-15mills(125-400um) roughing 2.5um fine finishing
9A60JV tool post grinding wheel
These guys might have better wheels.. https://cuttermasters.com/
Continental diamond tool https://www.cdtusa.net/ used by solid
rock..
radiac
Lapping machine
Alumina disk - out of chemical laboratory - used with diamond - 1um
as a charged lap for mirror finish - Stephans disk is only 100mm
he gets 1000grit(about 15um) for his first polish - near
mirror.. M5 screw hods it together. Wheels from search
terms "faceting lap" "Lapidary - gem polish" etc.. Don't get the
cheapest.
Also he touched up an insert with 1um diamond paste..
U2 Deckel style
D-bit grinder
Shars 101-1008
Wheels are ⌀4" outer diameter ⌀1.25" bore.
Gaskets
Sealers
Hylomar is the deal for close fitting things - solvent is
acetone. Maximum surface roughness target 2um-Ra
Ball bearings
Class 1, 3, 5, 7, and 9. The Higher ABEC classes provide better
precision, efficiency, and greater speed capabilities.
Lubricants
Liquidmoly LM 48 - assembly grease (Stefan likes it) for
chucks etc.. https://products.liqui-moly.com - or blue moly? For
assembly - not moly -- High-performance tungsten disulfide paste for
heavy-
duty applications. It adheres even to apparently smooth surfaces.
Rubbed into bearings and slideways, it prevents running-in damage
and seizing marks when assembling components with tight pair-
ings. Contains a synergistically active solid lubricant system with
a zinc sulfide, graphite, fluorides and tungsten disulfide base.
Operating temperature range: -35 °C to +450 °C.
One can also just mix some molybdenum disulfide in to a bearing
grease - I like the idea of the first lube having a bit of moly in
it.
Never-seize (AKA Never-sneeze) - Blue moly has more of moly -
molybdenum disulfide 7-13% and pure nickel powder 7-13% NLGI = 0.5 -
not for high speed bearings. The grit is abrasive - but keeps bolts
from seizing. 'Black moly' has even more molybdenum disulfide
10-30%. Zinc Oxide 5-10%. Don't use as assembly grease on
bearings.
Vactrac A better way oil? Harig oil16211245 http://www.trutech.store/harigstore/product.php?productid=17810
Penetrating schmoo
Commercial mixes of penetrating stuff don't penetrate quickly. Kroil
and WD40 can work, but the winner by a factor of 10 is something you
mix yourself. 50/50 solution of acetone and automatic transmission
fluid. It's a mixture not a solution so you have to shake well
before use. Apply liberally and it should loosen within 24 hours.
(has anyone tested this?).
MMO (Marvel
Mystery Oil) Lots of exaggerated claims - contains:
Petroleum distillates (hydrotreated heavy naphthenic) also known as
mineral oil, 74%
Petroleum distillates (Stoddard solvent) also known as white spirit,
25%
Tricresyl phosphate, an antiwear and extreme pressure additive in
lubricants 0.1–1.0% (an antiwear and extreme pressure
additive)
Ortho-dichlorobenzene, a softening and removing agent for
carbon-based contamination on metal surfaces, 0.1–1.0%
(high-boiling solvent)
Para-dichlorobenzene, a precursor used in the production of
chemically and thermally resistant polymers, <0.1% (moth
ball - preservative?)
Cutting lube -
coolants - schmoo
Aluminum routing - pure A-IPA mist - tiny amount - easy clean up.
Kool-Mist will spoil and plug up sprayers and stink - add tiny
amount of some ORTHO-BENZYL-P-CHLOROPHENOL (Lysol concentrate - out
of UK in 2020)
Make a heavy metal jar for schmoo - JIC hydralic cap and
plug -20 (1.25")
coconut oil - 0.5% boric acid (50nm particle size)
anchor lube
Kleen flo
rapid tap
QualiChem Quick Tap Extreme-Duty what Edge precision is using for
tapping.
Aluminum tap majic (Abom likes.)
Mistic Metal Mover (Abom likes for cutting stainless)
Stephan uses Jokisch Alpha 93 cutting oil - comes in aerosol (I
like)
https://www.blaser.com
makes very clear stuff - need to find out what is in
synthetics. https://www.qualichem.com
jokisch alpha 93 cutting oil ( Stephan) https://www.jokisch-fluids.de/catalog/en/metalworking-oils/cutting-oils/
https://www.hoffmann-group.com/GB/en/houk/Chemical-technical-products/Lubricating-coolants-cutting-materials/Cutting-oils/High-performance-cutting-oil-chlorine-free-Alpha-93/p/084210
qualichem tapping fluid - used by Peter Stanton
Lens cleaner - first contact
Viscous grease https://www.nyelubricants.com/damping
prevention
johnsons wax - chain wax??
Break Free CLP
ferrocote 5856 - source for small quantities???
Grease
Mobil Grease 28 - spindle ball bearings and ballscrew - thrust ball
bearings - think of this as ball bearing grease
Assembly grease - Liebherr Compund CTK -- Liqui Moly (20216 LM 48
Assembly Paste)
LTS-1 low temp - good water resistance aluminum
AP(All Purpose) Grease is a lithium based multifunctional high
temperature, water resistant grease
MP(Multi Purpose) grease number 2 grease?? washproof?
EP Grease(Extreme Pressure) EP grease has in its components, solid
lubricants (graphite and/or molybdenum disulfide) to provide
protection under heavy loadings.
NLGI consistency number (sometimes called “NLGI grade” or "NLGI
number") expresses a measure of the relative hardness of a grease
LUBE SPECS
Tables
LUBE CODE |
LUBE |
FS SPEC |
4 |
DRY |
NA |
12 |
WINSOR LUBE L-245X |
FS171A |
23 |
ANDOK C |
FS118 |
37 |
DOW CORNING 44 |
FS137A |
44 |
ANDOK 260 |
FS167E |
49 |
ANDOK B |
FS104A |
67 |
RHEOTEMP 500 |
FS208 |
76 |
KRYTOX 240AB |
FS452 |
78 |
CHEVRON SRI |
FS545 |
86 |
MOBIL 28 |
FS381A |
95 |
MOBILTEMP SHC 32 |
FS612 |
115 |
ISOFLEX TOPAS NB52 |
FS737 |
125 |
FERROCOTE 5856 BF |
FS639 |
149 |
ISOFLEX TOPAS NCA15 |
FS883 |
160 |
AEROSHELL 22 |
FS381B-P |
161 |
KRYTOX 240AC |
FS433 |
162 |
ISOFLEX NBU 15 |
FS637 |
167 |
WINSOR LUBE L1018 |
FS179A |
169 |
PQ CORROSION PREV. |
FS216 |
422 |
ISOFLEX SUPERLDS18 |
FS735 |
436 |
ANTICORIT L-245XBF |
FS890 |
443 |
ISOFLEX NCA 15 |
FS905 |
456 |
MOBILITH SHC15 |
FS919 |
NA |
LUBCON L252 |
FS915 |
NLGI
consistency
number |
ASTM worked (60 strokes)
penetration at 25 °C
tenths of a millimetre |
Appearance |
Consistency food analog |
000 |
445-475 |
fluid |
cooking oil |
00 |
400-430 |
semi-fluid |
apple sauce |
0 |
355-385 |
very soft |
brown mustard |
1 |
310-340 |
soft |
tomato paste |
2 |
265-295 |
"normal" grease |
peanut butter |
3 |
220-250 |
firm |
vegetable shortening |
4 |
175-205 |
very firm |
frozen yogurt |
5 |
130-160 |
hard |
smooth pate |
6 |
85-115 |
very hard |
cheddar cheese |
Thread issues
Recommended torque
Wrenches - fixed https://www.hoffmann-group.com/US/en/hus/Modular-machining/Indexable-milling-cutters-GARANT/Torque-screwdriver%2C-fixed-setting/p/211750?tId=281
Thread repair
Keenserts https://www.carrlane.com/product/threaded-inserts
Bolts work good for relocating a thread but for larger holes a
steel plug with Dutchman pins to lock
the repair plug in place.
Easily confused
threads
Key problem is that M10x1.0Keg thread is EASILY confused
with 1/8"NPT! 1/8"NPT is 27TPI - which works out to a pitch in the
metric world of 0.94MM which is close to the 1mm in M10x1.0Keg
threads. Keg comes from the German 'kegel' which means 'cone' -
thus tapered.. This easy confusion has led to 'No End of
Bad-Things'™
Painting
Improve wetting
Do wetting test
4 - ways to prep:
Comet cleanser
Sandblast if possible
Heat to 250-300C
Clean with TIG torch
All will no longer wet after a few hours. Wonder if this
helps with powder coating as well?
Degreasing and
stripping - rust removal
Solvents are a poor choice -
Best with an ultrasonic tank
TSPP(Tetra-Sodium-Pyro-Phosphate) will clean what the deodorized
kerosene solvents leave behind. This forms a Basic solution -
(just 1% gets one a pH around 10).
TSP(Tri-Sodium-phosphate) gets one to 1 pH of about 12 in a 1%
solution. One can remove even paint with it in a strong warm
solution. (Also used as a hard-soldering flux)
Both TSPP and TSP can attack aluminum - so you would want to be
quick and rinse well -
Purple power degreaser (wallymart)
Flash rust does not occur if the wetted surface is above Ph 8.2 or
so..
Citra-strip?
evaporust
Powder coating
Columbia coatings http://www.columbiacoatings.com/
DIY
powder coating 230C
Chrome http://www.columbiacoatings.com/store/p/1118-All-In-One-Chrome.aspx
powder on hot will fill holes..
Rust prevention
Storage coatings
Camphor in the tool chest
Boeshield - spray on wax.
Cold bluing
Clean and damp and warm - use RO water - active surface?
JAX makes gal jugs of it.
Hot bluing
Boric acid + mineral spirits paste - heat to red quench in oil -
polish
Heat over brass chips - blue and repeat
Clean and clean with 'rodico'
Thick brass box with brass shavings to make even heat.
Glass bead cabinet
150 micron
Makes surface wetable - good for painting
Tacoma upgrade kit for harbor freight cabinet http://www.tacomacompany.com/
Diamond coated glass - checkout scanners
70u after heat treatment aloxl
Files Vallorbe Swiss Habilis precision file http://www.vallorbe.com/en-ch/products/files/habilis-files
Diamond like coated glass:
Honneywell part numbers:
46-46807- Diamonex Platter for compact (420mm) (16.5") StratosH 2322.
46-46806- Diamonex Platter for full-size 508mm (20.0") StratosH 2320/2321.
46-00233 - Diamonex Platter - Compact Stratos 2421
46-00234- Diamonex Platter for sub-compact (353mm) (13.9") Stratos 2422.
46-00296- Diamonex Platter with lift handle for compact (399mm) Stratos 2421.
46-01085 - Diamonex Platter - 508mm StratosMS2430-105KD-US.
46-00235- Sapphire Platter for compact (399mm) Stratos 2421.
46-46809- Sapphire Platter for compact (420mm) StratosH 2322.
46-46808- Sapphire Platter for full-size (508mm) StratosH 2320/2321.
46-00236- Sapphire Platter for sub-compact (353mm) Stratos 2422.
46-00297- Sapphire Platter with lift handle for compact (399mm) Stratos 2421.
46-01127 -Sapphire Platter for StratosS and 2421 (399mm) with 3 flip ups.
Bandsaws
Chinese
Thing Everyone has
6-8 tooth (Stephan)
1/2 x 0.025 x 64-1/2 in. - AKA 5' 4.5" silly legacy units
DM2 (DieMaster-2) - bi-metal - 0.025
Skil 3386
length 150.5 151mm [59-1/4 - 59-1/2]
Bimetal in 9.5mm [3/8"] for metal - not including steel.
Roll-In Band Saw -
Model EF1459
Dream machine
Clamps
Holex Universal clamp (kant twist but better) https://www.hoffmann-group.com/PT/en/hop/Hand-and-assembly-tools/Clamps/c/86
Die / spindle
Grinder
BIAX make air powered 60k -100k RPM Biax? only air -
top end 85-100krpm
NSK pencil grinder dr-500 (Edge precision)
https://proxxon.com
- only goes up to 20k rpm - good dremel replacement TIR=
50um
https://store.cncstepusa.com/products/kress-1050-fme-p
kress
1050 FME-P runout of max 10um guaranteed.
https://www.nsk-nakanishi.co.jp/industrial-eng/mgt/emaxevolution/
Stephan's latest IR-310 https://www.artcotools.com/nsk-nakanishi-ir310-ring-type-attachment.html
Spindle air
grinder
PLANET 600 Air Turbine Spindle - 65,000 TIR = 1um
!! ($1000+ used as of 2020) rpm http://www.nskamericacorp.com/product/category/planet/28?AspxAutoDetectCookieSupport=1
Continental Diamond Tool Corporation https://www.cdtusa.net/
CBN grinding tools..
http://professionalinstrumentscompany.com/products/rotary-motion/air-bearings/
Air Turbine 602JS 40-90krpm TIR = 10um
U2 grinding
machine
Chucks
Rohm the best?
Albrecht chucks keyless look very good
ER Collets Notes
ER(Extended Range) originated by Rego-Fix - Swiss
company - originated in 1976.
The collet HAS to be snapped in before tightening.
Do not use the backup screw to set length - it is tightened AFTER
the collet.
ER Torque
collet size
|
Torque
recommended
|
Torque
max
|
Wrench
size
|
Range
|
ER8
|
|
|
|
|
ER11
|
|
|
|
|
ER16
|
28 Nm
|
50 Nm
|
25 mm 24.5?
|
1 -10mm
|
ER20
|
|
|
|
|
ER25
|
|
|
|
|
ER32
|
70 Nm
|
105 Nm
|
45 mm
|
2-20mm
|
ER40
|
120 Nm
|
150 Nm
|
57 mm
|
3-26mm
|
ER50
|
|
|
|
|
Metrology
Indicator Stands
The best surface plate indicator stand is the Murkens
tool (What Herman Schmidt sold and then copied). http://murkensprecisiontool.com/indicatorbase.html
Magnetic bases are not all the same. Be sure to look at the
pull strength. Often it is best to mill a flat where the main
rod screw in to make a stiffer joint - perhaps a copper crush
washer? And while you are at it, increase the diameter of the first
rod.
The Noga style arms have a trick for those new to using them - the
joints get tight one at a time as you tighten it. Still a bit
fiddly to use and they are not perfectly rigid.
Repeatometer
low carbon precision ground stock 1/2 x 4 x 11.75
The silicon nitride ball is 0.1875" diameter and is glued in a ball
milled pocket.
Flatness by
process and example - approximate
- Milling 10um
- Surface grinding 2um
- Commercial optics - 2.5um - spectacles - prisms
- Scraping cut - 2um
- Surface-plate - 2 - 8um - best small 900nm - light wave
length
- High quality optics 250nm -
- Gauge block flatness - 100nm - ability to wring ..
- Red light 600nm - 632.8nm popular red neon line
- blue light 450nm
- lapping 30nm - close to 1/20 wave
Scraping
Scraping cut - 2um
Normally cast iron.
DIY scraping tool inserts:
3/4 x 3/4 x 3/16
1/2 x 1/2 x 1/8
bar 3/16 x 3/4 cold rolled flat bar
M6 screw holding?
1/8 x 1/2 x 1" USA-Made C2 carbide blanks - MSC # 04120754 or
better carbide processors
Scraper blades are usually straight C-2.
Pin pointing scraper
https://youtu.be/QUtH8Wkhrw4?t=2804
Blade for scraping carbon-steel as per Alex Fillafer
Surface Plate
notes
Inking
Spotting ink - charbonnel aqua wash https://www.dickblick.com
PRussian blue
primrose yellow
cardinal red
Robin renzetti says 50:50 charbonnel/Canode mix in a syringe is the
bomb- use with latex rubber rollers.
Support blocks
for surface plates
Bessel points located .2203 X L from each end --- .5594 x L apart -
equalized deflection by gravity - middle and ends
Airy points = no slope at ends 0.21132* L from each end or .57736
apart
That being said - I think using 3 points under a surface plate
ignores reality. A somewhat compliant flat material that
supports the plate all over will allow the plate to hold more weight
without bending. Anyone can load this up in a CAD system and
run FIA to see the truth.
Materials in
plates
SiO2 In the form of Alpha-quartz (7moh) - 5.5 x 10-7 /°C
= This coefficient is 1/34 that of copper and only 1/7 of
borosilicate glass.
SiC - 4.4X10-6/°C
Cera Zero 826HV *
Possible treatment
to make black plates surface wear better
There is a technology used on concrete floors - sodium
silicate(water-glass) is applied as a densifier (sometimes lithium
silicate) - then diamond polished to a shinny surface.
Black surface plates are stiffer, but softer surface.
I propose coating the surface with sodium silicate to provide a
harder wear surface - then lapp flat again. Could be it will
be too smooth - cause wringing problems?
Setup blocks
Setup blocks
20x40x60mm
Renzetti hole pattern 6mm thread
Squish-test
Plastigauge - -- I have used multicore solder with accurate
results as well. Just squish the solder - measure with
micrometer.
Temperature
Thermochrom temp crayons.
Using Straight
edge
There is more to this than meets the eye(pun intended).. See http://what-when-how.com/ology/straight-edges-metrology/
Plastics and
similar materials
Ren Shape 5045 is our highest density polyurethane
foam board - sacrificial plate for routing - etc.
PTFE(teflon)
Epoxy epi- + oxy Epoxy - bisphenol A diglycidyl ether (Bisphenol is
a phenol) - there is a strained triangular ring - with an oxygen
(the oxy of epoxy) and two phenol rings (Phenols like to bond to
everything (thus why rather than their so-call antiox properties -
they bond to metals preventing absorption)).
TPU92A - filament - o-rings etc. Flexable
PLA - brittle
PETG (PET - Glycol-modified) - good layer adhesion - Lower
temp
Nylon Strong
Metals
Detect, identify
metal type - end-paint color codes
Hit with hard knocker:
Steel will go RINGGGGGGGGGgggggggg.......
ductile iron will go DING..
cast iron will go THUD.
https://www.europa-lehrmittel.de/tm47
Detect cast iron from cast steel - dust vs chips
01 tool steel = drill rod
Grinding tests - White, pink, ruby-red, or beige colored wheels work
best - not the cheap black ones
See spark-tests
Carbide is heavier than HSS - 14-15g/cm^3 vs a little less than
8gm/cm^2
End paint color
codes
There is more than one standard.
Not a good idea to rely on it. Often found on end of bar stock.
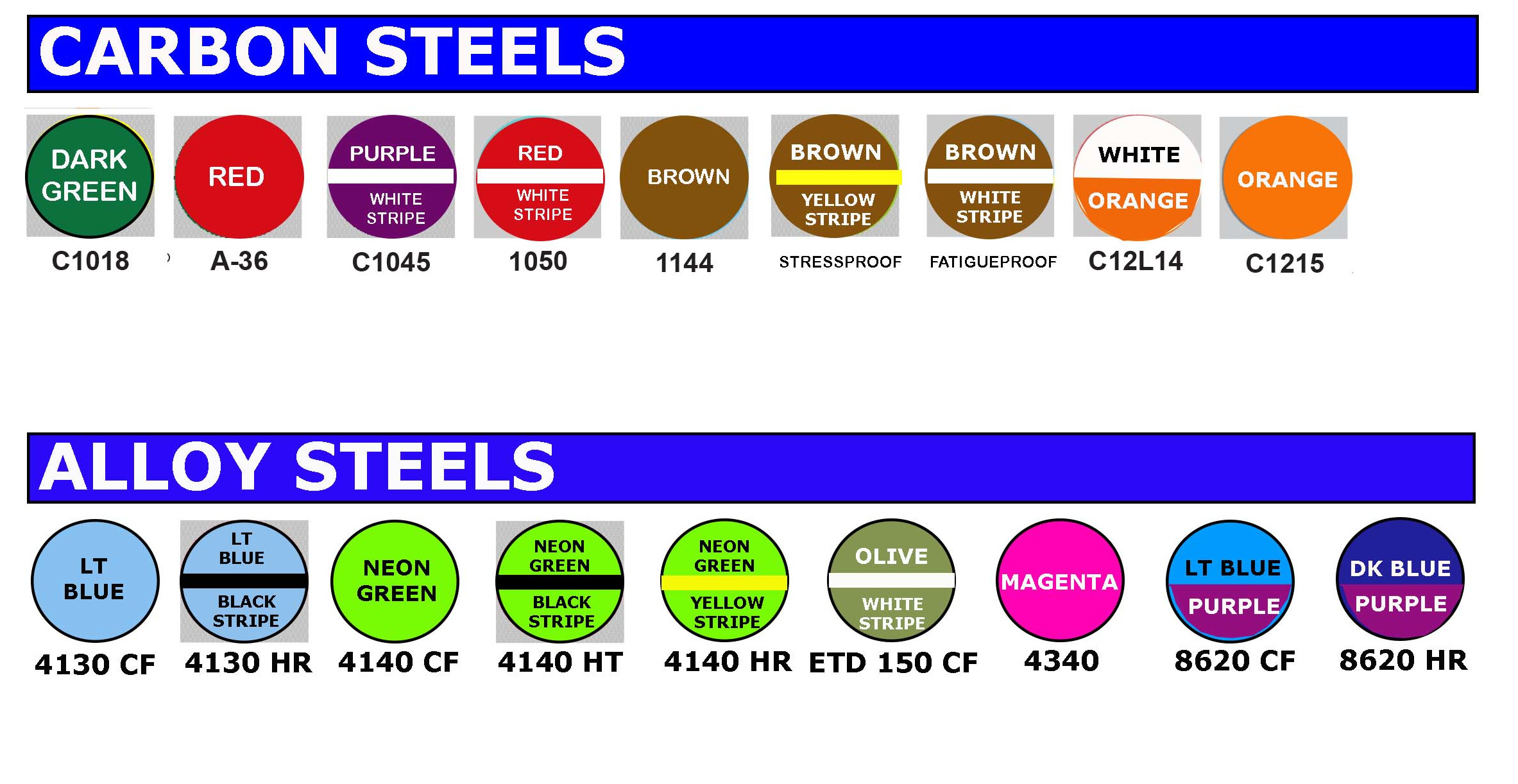
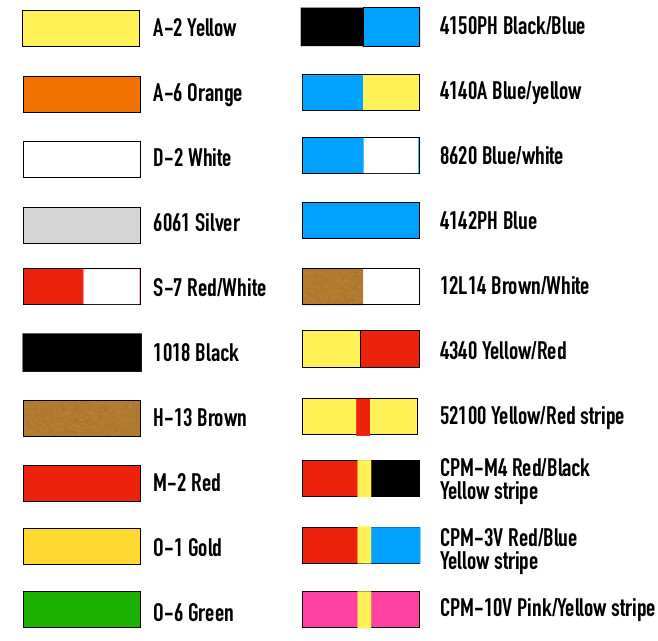
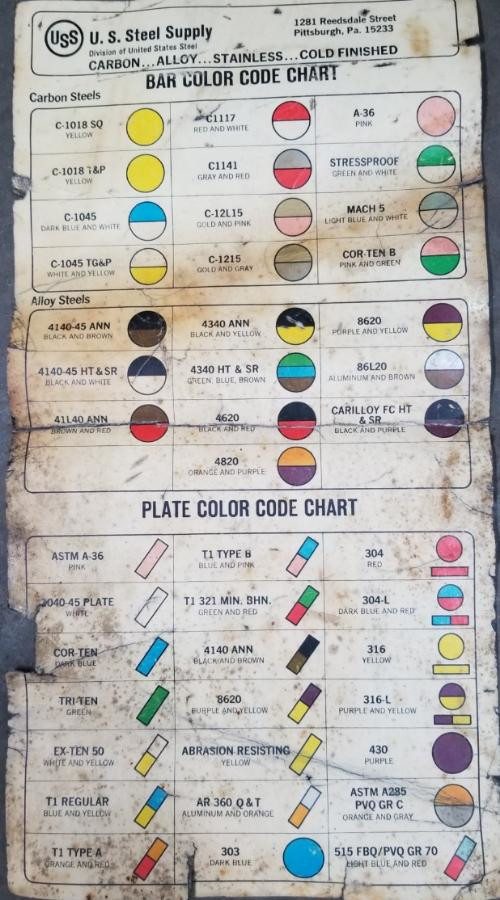
Sources
Special alloys
http://www.nealloys.com/
https://www.frysteel.com/products.php
Cast iron
Durobar is much the same - machines better - better finish - MUCH
more expensive than regular cast-iron.
Steel
Most common steels
1020 gummy mild steel
4140
O1
D2
A2
Mild Steel
1018 has a higher manganese content than certain other low carbon
grades, such as 1020. With higher manganese, 1018 is better steel
for carburized parts, since it produces a harder and more uniform
case. It also has higher mechanical properties and better
machinability due to the cold drawing process
ALLOY STEEL
Steel grade cross reference - Which standard to use? Din
W-Nr(Werkstoff-Number) - SAE/ANSI ???? Have a Material Cross Reference List
pdf Just a start..
Need to make a table - columns - SAE - W-rn DIN Description
O1 Drill rod (oil hardened) - 115CrV3 DIN 1.2210 / 115CrV3
4140 - DIN 1.7225
A2080 tool steel
DIN 1.2080 tool-steel (D3) - X210Cr12 D3 is an oil hardening,
high carbon/chromium type tool steel with very high wear resistance.
It hardens with a very slight change in
size. The alloy possesses very high compressive strength and is deep
hardening.
DIN 1.2379 tool steel (D2) - X 153 CrMoV 12
≈ 720 N/mm² high-alloy steel for through-hardening with
moderate machinability; extremely wear resistant and low warpage,
good dimensional stability, toughness and through hardenability
A2 - A2 Tool Steel | 1.2363 | X100CrMoV5
A2 Tool Steel is a versatile, air hardening chromium alloy tool
steel that replaces O1 tool steel when safer hardening, less
distortion and increased wear resistance are required. AISI type A2
steel is intermediate in wear resistance between O1 oil-hardening
tool steel and D2 high-carbon, high-chromium tool steel.
Toolox® 33 is a prehardened steel suitable for tools and engineering
components. It possesses good dimensional stability after machining.
Delivered in quenched and tempered condition, Toolox® 33 features
high impact toughness and very low residual stresses to achieve good
dimensional stability after machining.
C45 (1045) Steel for making medium carbon tools.
4037 - dowel pins
https://www.steelforge.com/alloy-steel-4037-aisi-4037 Molybdenum
Din 100Cr6 ball bearing steel SAE 52100
DC-53 Tool Steel
Din W-Nr(Werkstoff-Number) e.g. 1.4404 ( this would be an AISI
SS316L, DIN X2CrNiMo17-12-2, UNS S31603 etc.
- Higher hardness (62-64 HRc) than D2 after heat treatment
- Twice the toughness of D2 with superior wear resistance
- Substantially higher fatigue strength compared to D2
- Smaller primary carbides than D2 protect the die from
chipping and cracking
- Machines and grinds up to 40% faster than D2
- Less residual stress after wire EDM
8620 20NiCrMo2-2 C=.2% Mo=.2% is a hardenable chromium,
molybdenum, nickel low alloy steel often used for carburizing to
develop a case-hardened part.
Alloy composition (by weight)
SAE grade |
% >Cr |
% Mo |
% C * |
% Mn |
% P(max) |
% S(max) |
% Si |
4118 |
0.40–0.60 |
0.08–0.15 |
0.18–0.23 |
0.70–0.90 |
0.035 |
0.040 |
0.15–0.35 |
4120 |
0.40–0.60 |
0.13–0.20 |
0.18–0.23 |
0.90–1.20 |
0.035 |
0.040 |
0.15–0.35 |
4121 |
0.45–0.65 |
0.20–0.30 |
0.18–0.23 |
0.75–1.00 |
0.035 |
0.040 |
0.15–0.35 |
4130 |
0.80–1.10 |
0.15–0.25 |
0.28–0.33 |
0.40–0.60 |
0.035 |
0.040 |
0.15–0.35 |
4135 |
0.80–1.10 |
0.15–0.25 |
0.33–0.38 |
0.70–0.90 |
0.035 |
0.040 |
0.15–0.35 |
4137 |
0.80–1.10 |
0.15–0.25 |
0.35–0.40 |
0.70–0.90 |
0.035 |
0.040 |
0.15–0.35 |
4140 |
0.80–1.10 |
0.15–0.25 |
0.38–0.43 |
0.75–1.00 |
0.035 |
0.040 |
0.15–0.35 |
4142 |
0.80–1.10 |
0.15–0.25 |
0.40–0.45 |
0.75–1.00 |
0.035 |
0.040 |
0.15–0.35 |
4145 |
0.80–1.10 |
0.15–0.25 |
0.43–0.48 |
0.75–1.00 |
0.035 |
0.040 |
0.15–0.35 |
4147 |
0.80–1.10 |
0.15–0.25 |
0.45–0.50 |
0.75–1.00 |
0.035 |
0.040 |
0.15–0.35 |
4150 |
0.80–1.10 |
0.15–0.25 |
0.48–0.53 |
0.75–1.00 |
0.035 |
0.040 |
0.15–0.35 |
4161 |
0.70–0.90 |
0.25–0.35 |
0.56–0.64 |
0.75–1.00 |
0.035 |
0.040 |
0.15–0.35 |
* The carbon composition of the
alloy is denoted by the last two digits of the SAE
specification number, in hundredths of a percent |
C1084 - forging steel - rail track
ANCI C1060 - medium carbon steel C = .55-.65 Mn 0.6-0.9 P
.04max S 0.05 max knuckle pin
TOOLOX 33 - quenched and tempered tool steel designed to have low
residual stresses. It is characterized by its extremely good
machinability and is pre-hardened to 33 HRC.
Gauge blocks are made of 52100 (chromium alloy steel ) tempered to
66 Rc W-nr. 1.3505 - DIN 100Cr6
A6 Cams
M2 Dills/end-mills (HSS?), kinives, taps
S2 bolt cutters, wrenches
S5
S7 Cams,
O2 taps
O6
L6 15n20 - (1075 +2% nickle) chisels, hammers, screw
drivers, wrenches
W2 files
AN25
In 10xx - the xx stands for the hundredths of a percent carbon. 1020
- would be 0.20% carbon
Framing nails 1008/1010/1018
1018 - most common grade
1020 -1030 railroad spikes, brake lever,
1040 - bolts, connecting rods, tubing
1050, and 1541H - Car axles below 1.625"
1060 Snap rings, railroad knuckle pins
1070 cluch disk,
1075-1095 - carbon kitchen knives - will rust - but get sharp.
1084 or higher - Railroad tracks.
1085 mower knives, music wire?
1095 - clock-spring-steel - Usually tempered blue - some drywall
knives
1145 - Ujoints
2330 heat treated bolts
3130 Steering ARm bolts
3115 transmission gears
4042 Steering arms
4063 coil springs - car
4140 - 4145 hydraulic ram, transmission shafts
440C Corrosion resistant ball bearings.
4815 heayduty bolts
5160 is used to make leaf springs, coil spings-truck, scrapers,
bumpers, flexible knife edges.
52100 Ball bearings
carbon steel razor blades - about 1.2% carbon
For Machine shafts
and parts - hardening etc
When you want tough materials that will see high tensile stresses,
loads in alternating directions and magnitudes, you're going to have
to rely on heat treated carbon or other alloy steel.
SAE8620 or equivalent is good - harden (carburize) prior to
grinding.
SAE4150 machined in an initially normalized condition. If you
subsequently harden and draw to HRC 40-42 -- tough and strong.
Precise bearing fits on the spindle, need finish grinding to size.
Bearing fit will be depend on type of bearings used.
Hang shafts when heat treating. When quenching, dip quench AXIALLY
to avoid the risk of bowing/bending the part.
Surface hardening puts the subsurface into a compressive load which
enhances strength and toughness. Explains why gears are often made
of carberized and hardened 4820 or 8620 or 9310.
8620 makes EXCELLENT gears and shafting material. It is both tough
and wear resistant, especially when deep carbuized. It is also
relatively inexpensive. For really GOOD stuff, ask for AQBQ grade
(aircraft quality, bearing quality). This stuff is comparatively
void and stringer free. It also comes with material certifications
that the imported crap doesn't have.
To really optimize stress reduction/minimization in a part:
1. Stress relieve at 1200F for 1-2 hours at heat prior to heat
treating. Furnace cool if possible.
2. Carburize while standing on edge or hanging in furnace to
minimize warpage.
3. Quench via axial dip as opposed to laying on side while
quenching.
4. Double temper prior to grinding
5. Stress relieve at 250-300F after finish grind.
6 - to selectively carburize use copper plating (about 50um
thick) before carburizing.
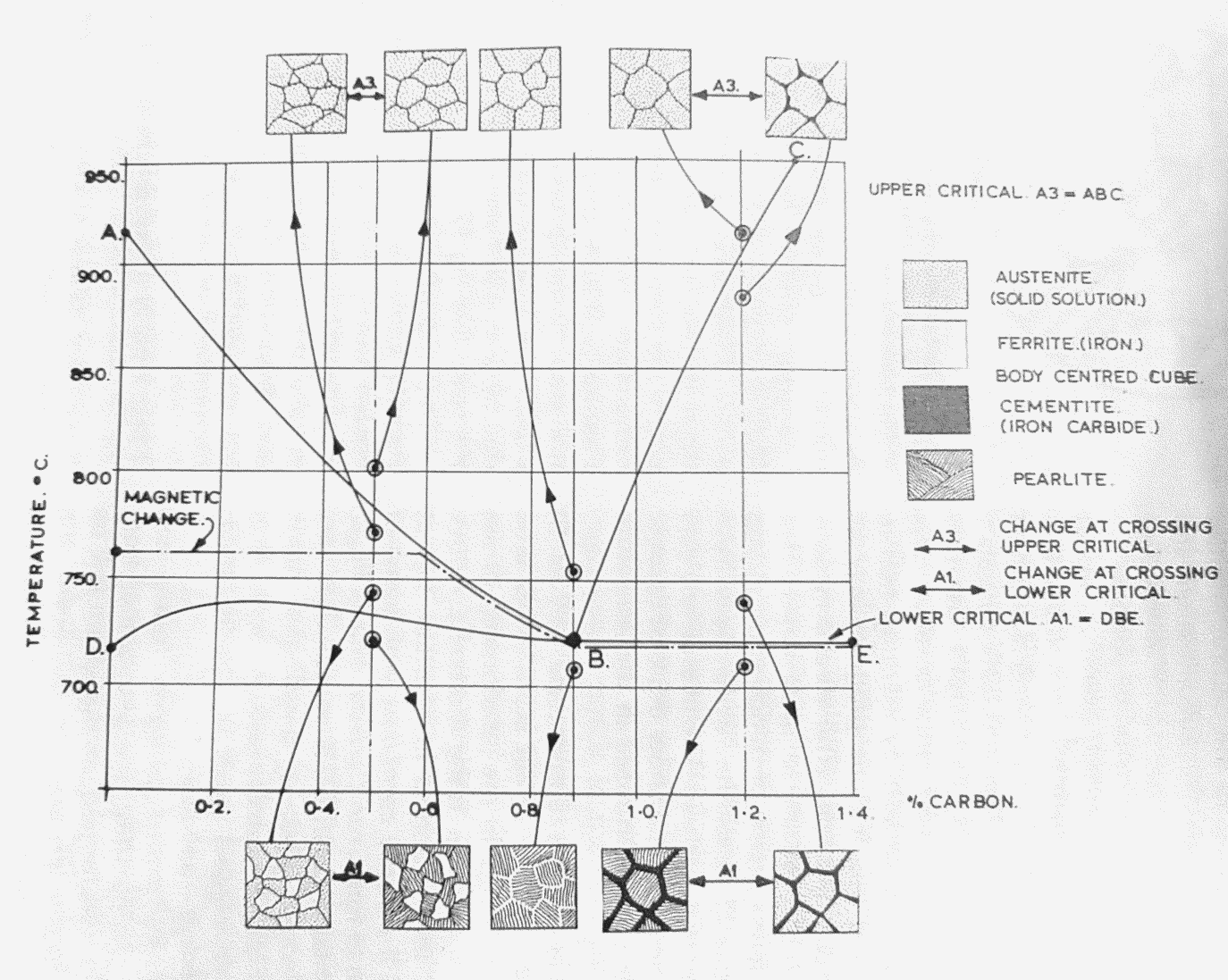
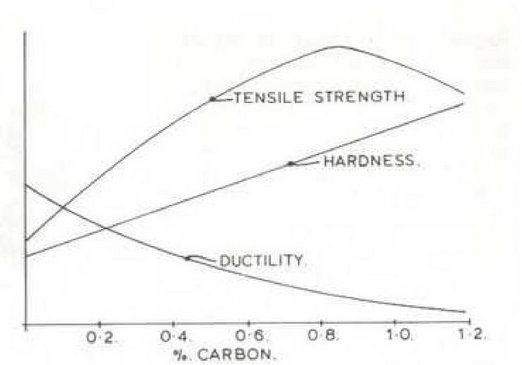
See
Hardening, tempering
and heat treatment. Workshop practice series
Heat treating -
carbonizing
plasma carbon nitriding
(temper)
vacuum temper, deep freeze - service from Solar Atmospheres
One can mix boric acid with methanol - heat part in steel bowl -
then quench bowl and all - no scale to speak of. A thinner mix
can be used to coat parts.. Borax is NOT boric acid.
Hardness
Rc hardness. Tool
42 Socket head cap screw
49 scales - metal rulers
49 screwdriver blade
50 hex wrench
55 lock-in pliers
56 pocket knife blade
58 height scribe blade
58 barbers razor blade
59 dowel pin
65 file
65 high speed steel
79 micro grain carbide
Stainless
Minimum of 10.5% chromium. The chromium forms a protective oxide
film on the surface - very thin (2-3 nm).
Ferritic - (Cr 12.5 -17%) mostly nickel free - not heat treatable -
weldable(thin) - magnetic
Martensitic (C - 0.2-1% Cr 10.5-18%) Heat treatable - magnetic -
hard to weld - can get brittle
Austenitic (Cr 16-26% Ni 6-12% +) Most common - non hardenable
- work hardenable - weldable mostly non-magnetic
Duplex (Cr 18-26% Ni 4-7% Mo 0-4% cu ) magnetic,
http://www.sidecuts.com/
Sheet steel stock gauge 18 and 10
Stainless sheet 17-7 - easy to harden
Martensiticstainless steels can be heat treated and hardened, but
have reduced chemical resistance
ISO14305 (AKA 303)most easy to machine austenitic grade of stainless
- has Sulfur for machine-ability.
https://titussteel.com/our-products/mold-and-die-steels/tool-ox-33/
Brass
Online metals has several types
360 brass Zn35.5 Fe 0.35 Pb 2.5-3.7 - most common of rod and bar
Bronze
Aluminum Bronze
642
This is a great material that is harder than Aluminum or bronze and
machines well. We have used it for a great number of projects. Is an
excellent material for valve stems, gears, marine hardware,
pole-line hardware, bolts, nuts, valve bodies and components,
mechanical parts
Gilding metal
cu90 zn10 - annealed rockwell-F 53
copper
hadness - annealed 40HV - hard 110HV
Aluminum
356 - used for casting..
Higher the number the stiffer the aluminum -
7075 - quite strong - but poor to weld
cutting tools
Feeds and speeds
Feeds: Cutting speed or surface speed or speed - tooth tip speed
= Vf
Speeds: Feedrate or feed - table speed
Surface finish - to improve from most to least effective -
increase surface speed - increase depth of cut - increase feed
rate
From tool/insert
data - printed on package is Fz and Vc
we can calculate n(spindle speed) and Vf (speed
of table.
Fz or Ft = Feed per tooth (chip
load) in mm = MMPT (millimeter/tooth) (imperial
IPT Inch per Tooth)
Vc = m/min (cutting speed - tip of tooth speed)
in m so don't confuse with millimeter mm!!! SMM Cutting
speed - surface-distance-per min
D = tool diameter in mm (in turning - workpiece diameter )
n = rev/min as in RPM becomes S-code
- n = 1000 ·Vc / D · π · n Simplifies to Vc
318/D
Vf or Fm = table feed = velocity of
table MMPM (Millimeters per minute) (endmill) in
mm/min Table feed this is the F-code
Where:
Z or N= number of teeth or flutes
n = Vc · 1000/π · D · n
Vf or Fm = table feed = feed rate =
velocity of table MMPM (Millimeters per minute)
Ae = width of cut or Radial depth of cut
Ap = Depth of cut, Axial Depth of cut.
D1 = diameter of shaft without the flutes.
Chipload = feed per tooth
n = rev/min as in RPM n = Vc
1000/D π Simplifies to Vc 318/D
Fn = Feed per rev as in MMPR (Millimeters Per
Revolution)
SMM Surface meter/min (imperial SFM (surface Feet per
min)) = π D n
Vc = π · D · n /1000 (1000 is to
convert m to mm)
Fz = Vf / Z · n
Vf = Fz · n (drill)
f = feed per rev (mm/rev)
Cutting feed (m/rev) x spindle speed (RPM) = feed
rate m/min
End-mill plunge rate = feedrate/flutes
Q = material removal rate (cm3/min)
Ra = surface roughness (μm)
hm = average chip thickness. = fz (Ae/D1)1/2
For best surface finish - step-over should = feed per
tooth.
Spotting drill
Some use a split carbide with a point angle to match the drill.
Some use a pyramid point carbide (the math to get the angle right
is harder). Both of these are similar to the points used for
engraving, but the spot drills are of much larger diameter - all
are stubby.
Boring heads
WOHLHAUPTER boring head -
Schmidt makes small ones http://www.schmid-praezision.de/eng/?Products-and-Service/Facing--and-Boring-Heads/UBS-Universal-Facing-and-Boring-Head
ausdrehkopf
Iscar DR-MF-08R-2.25D-12A-04 https://www.iscar.com/Products.aspx/CountryID/1/ProductId/4906
What Peter Stanto uses - actually a d'andrea rebranded.
$500-$700/2020
Inserts
Lots of suppliers - Mil-Tec inserts - might be the best?
S-PS-032-5-2TA -- PS032-MTC357A2 ph(800) 564-5832
Insert Size and
shapes
ANSI vs ISO - The
codes will confuse you
Particularly the number bit - the first letters can be exactly the
same - but for instance - an ANSI CDE322 works out to be a ISO
CDE160308. In a sane world, the codes would put the most
variable parts at the end - so Shape, dimensions - then angles -
then tolerance and grade codes would have PMK codes embedded....
Well we don't live in a sane world.. There are extra letters added
by some makers to make sure you stay confused.
See insert
codes for details or this chart with ISO, ANSI, and tool holder
codes.
This table
helps one translate ISO numbers with ANSI numbers.
Current Insets
S20R-SCLCRO9 (Insert CCMTO09T304)
SNRO020R16 (Insert 16IR AG60)
SER2020K16 (Insert 16ER AG60)
SDNCN2020K11 (Insert DCMT11T304)
SDJCR2020K11 (Insert DCMT11T304
MGEHR2020-3 (Insert MGMN300)
SCLCR2020K09 (Insert CCMTO09T304)
WWLNR2020K08 (Insert WN □ □ 0804 □ □ )
Find a boot-leg copy of ISO-1832-2017 for the latest bits.
And here is an example of the Old ANSI standard
CDE 322R05
|C 78 or 80° shape
||D 15° clearance angle
|||E Tolerance
||| - blank
|||||3 3/8" inscribed circle
||||||2 2/16" thickness
|||||||2 2/64" radius
||||||||R Right hand
|||||||||05
DCMT and CCMT are shapes- Details here http://www.carbidedepot.com/formulas-insert-d.htm
holders
Lathe cut-off
Iscar SGFH 26-3 Uses Insert : GFN/R/L 3
Lathe others
Cutting tool
materials
Inserts Carbide
PCD Poly Crystalline diamond aluminum and copper
CBN Cubic Boron Nitride - really hard - harder than diamond at
high temperature. Can actually machine sintered carbide to some
extent.
Carbide" is mostly Tungsten Carbide (WC) sintered with cobalt as
a glue to hold it together. - Straight grades (C1, C2, C3, C4) are
tungsten carbide. C5 through C9 are alloyed grades containing
titanium carbide, niobium carbide, tantalum carbide and a few
others also in varying percentages. Each added for certain
characteristics and often only 1 to 5 percent of each. These are
also know as "steel cutting grades" while the C1-C4 numbers are
sometimes called "cast iron and/or aluminum" grades. C-8 or 9 may
be 25% or more TiC so pushing a cermet. Grades above C-9 are
special use and mostly straights. You see them in hammers, dies
and such.
Tungsten Carbide Standard Grade Chart |
Industry Code |
FCC Grade |
Binder Content & Type |
Hardness (Ra) |
Hardness
(HV30) |
Density (g/cm3) |
Minimum Transverse Rupture Strength (psi) |
Grain Size |
General Purpose Grades |
C2 |
FC3 |
6% Co |
92.0 |
1585 |
14.95 |
320,000 |
Fine |
C1 |
FC4 |
7.5% Co |
91.0 |
1460 |
14.70 |
330,000 |
Fine |
Metal Forming and Wear Grades |
C10 |
FC10 |
9% Co |
90.0 |
1360 |
14.60 |
360,000 |
Medium |
C11 |
FC11 |
12% Co |
89.5 |
1315 |
14.30 |
390,000 |
Medium |
C12 |
FC12 |
15% Co |
88.0 |
1190 |
14.00 |
420,000 |
Medium |
C13 |
FC13 |
20% Co |
85.0 |
955 |
13.60 |
450,000 |
Medium |
C14 |
FC25 |
25% Co |
83.2 |
760 |
13.15 |
435,000 |
Medium |
Submicron Grades |
C3 |
FC3M |
6% Co |
93.0 |
1740 |
14.95 |
375,000 |
Submicron |
C2 |
FC10M |
10% Co |
91.9 |
1570 |
14.50 |
450,000 |
Submicron |
C1 |
FC12M |
15% Co |
89.5 |
1315 |
14.00 |
530,000 |
Submicron |
Rotary Drilling and Mining Grades |
C11 |
FC10C |
10% Co |
88.6 |
1240 |
14.50 |
400,000 |
Coarse |
C12 |
FC11C |
10% Co |
87.8 |
1175 |
14.50 |
425,000 |
Coarse |
Corrosion Resistant Grades |
- |
FC3N |
6% Ni |
91.0 |
1460 |
14.95 |
275,000 |
Fine |
- |
FC10N |
9% Ni |
89.5 |
1315 |
14.60 |
290,000 |
Fine |
- |
FC8N |
8.5% Ni |
91.5 |
1515 |
14.50 |
300,000 |
Fine |
- |
FC82 |
15% Ni+Co |
89.9 |
1355 |
9.00 |
310,000 |
Fine |
C6 - common
|
|
|
|
|
|
|
|
C1: Good wear resistance, nonferrous drawing, light blanking
dies, mandrels, wear rings, high pressure parts, wood working
blades, valve stems and seats, knives, bearings, grippers and
guides.
C2: General Purpose wear resistance, where only light shock is
encountered; small dies and mandrels, nonferrous wire and tube
drawing, nozzles, seal rings and powder compacting dies.
C3: High abrasion resistance, little shock resistance; small
drawing dies, coating and compacting dies, bushings, machines
parts and valve parts.
C4: Hardest grade, high wear resistance, no shock or impact
encountered; wear bushings and nozzles.
Cermet is a composite material composed of ceramic (cer) and
metal (met) materials.
CBN
MKD
(Monocrystalline Diamond)
Insert screws
; CDE322 takes a 60° flat head 6-32 - slightly less than
0.5". This is notated as SE-02-01 or SE-02-11 - the last
number is something about the length - but not clear what.
Wish I knew where to find the standard this is all based on.
Grades
First understand the PMK codes:
See machine reference folder
Sandvik codes start with GC ( Grade Code)
We update the second number when a new generation is created, so
for the 3020 it would now be 3220 or GC3220
GC3040 also cast iron.
H13A non ferris
https://www.sandvik.coromant.com/en-us/products/pages/milling-inserts-grades.aspx
https://www.ingersoll-imc.com/support/milling-grades
https://www.ingersoll-imc.com/support/turning-grades-cross-reference
https://www.sumitool.com/en/downloads/cutting-tools/general-catalog/assets/pdf/GC_A_en.pdf
https://www.machiningdoctor.com/grades/grades-finder/
https://www.cets.com/resources/kennametal-grade-descriptions.html
This table can help cross
insert grade codes.
Ingersol old
codes
Some crosses
https://www.widia.com/us/en/resources/conversion-guide.html
IN2505 P20-P30 M20-M40 K20-K30 N10-N30 S20-S30 H10-H30
IN2530 P20-P50 M20-M40 S20-S40
10K - H13A - K
102 KNSM20-M40, P20-P50, S20-S40
108 PMS
Grade 111 --> IN10K - K
227 P-M-S
305 P
501 K
511XL P
555 P-M-S
6510 K
6530 P25-45 M25-40
581 à IN1530 à IN2530 PM
205 à IN15K cast iron but HiPos lines went to IN30M -
N
301 à IN5530 à IN6530 à IN2530 P
919 CVD coated - 20 years old. likely something like what would
eventually become IN6510 or IN6530 K
IN2515 would be the cast iron grade K?
IN15K N
ISCAR codes
IC70 P15-25 c6
IC350 P10-20M K10-30
IC354 P20-40 M10-30 KNSH
IC328 PMS
IC656 P20-40 MKSH
IC907 P10-30 M5-20 K15-30 H05-15 S05-20 N05-20
(Iscar SGFH 26-3 Uses Insert : GFN/R/L 3)
Mitsubishi
U610 PK
UE6020
PK
US735
VP15TF P20-30 M20-30 K20-30 S10-20
Sandnvik
4325 P
435 P35
H13A N15-30
3020 K15, P15 CVD COATED K(fz 0.10-0.21mm Vc
225-185m/min)H(fz 0.10-0.21mm Vc 45-60m/min)
4015(GC4015) P-1-30 K5-25
5015 P K
Kennametal
CM3
KC725M P30-40 M30-40 S30-40
KC850 P25-45 M30-45 C5-C6
K313 M10-20 K05-20 N10-20 S10-20 C3-C4
KY2100
Korloy
PC9030 intended for M ft=0.05mm/ Vf=90mm/min
Kyocera
TN60 P1-10 M1-10 K1-15
TC60 - PM
Tungaloy
N308 P M
Unknown
YBM251 (ISO Class: P15-P40, M10-M30)
CK251 - appears to be YBC251 P10-P30
Chinese
grades
Coatings
CVD(ChemicalVaporDeposition)
CVD coatings are thick (typically 9 – 20 microns) and highly
wear resistant, making them especially useful for steel and cast
iron machining as well as widely used in turning operations. Such
thick coatings can compromise edge toughness. Good for
turning, milling and drilling applications involving ferrous
materials. In fact, CVD-coated inserts are recommended over
PVD-coated inserts for turning, milling or drilling steels and
cast irons.
TiN Coatings:
Excellent build-up edge resistance
Excellent on gummy materials
Excellent for threading and cutoff operations
Makes it easy to identify what insert corners have been used
Effective at lower speeds
TiC Coatings:
Excellent wear resistance
Effective at medium speeds
Excellent on abrasive materials
Al203 Coatings:
Excellent crater resistance
Effective at high speeds and high heat conditions
PVD (PhysicalVaporDeposition)
PVD coatings are thin (typically 2 – 3 microns) yet tougher and
typically smoother than CVD coatings. Useful for machining
materials, such as superalloys, titanium alloys and
difficult-to-machine stainless steels, that typically notch or
chip cutting edges.
PVD-coated inserts are especially useful for turning, milling and
drilling applications involving high-temperature alloys, titanium
alloys and stainless steel. PVD-coated inserts are recommended
when turning high-temperature alloys; however, if the alloy is on
the softer side and can be machined at higher speeds, a CVD
coating is preferred.
PVD Coating Types:
TiN Coatings:
Excellent built-up edge resistance
Broad application range
Effective on high-temperature alloys
Effective on stainless steels
TiCN Coatings:
Harder than TiN coatings
Effective on end mills
Sometimes used in milling applications where the work material is
abrasive
TiAIN Coatings:
Harder and more stable than other PVD coating types
Becomes harder and more stable with time
Effective on high-temperature alloys and stainless steels
Gears
module-number = outside diameter/ (number-of-teeth + 2) in
mm of course.. To convert to obsolete imperial numbers
= 25.4 /module-number
Bearings
Lip seals create more heat than you would think..
Fasteners
For button head screw - torx-plus is the best - hex drive
fails. Torx-plus should probably be the default for most
socket head fasteners.
CAD And CAM
Robenz robinrenzetti uses solidworks CAD
Stephan uses Autodesk Fusion CAD (pro E at work)- Linux CNC
CAM - BOBCAD - I think alibre ..
Yes: Big step for me, had to pull the trigger on a 3d cam
package to go along with Alibre Designer. Tried different packages
in my price range and talked to several long time users (you know
who you are, thanks!), and I ended up buying Bobcad v32 in 3axis,
Pro version. Already using it to work in customer parts, with
multiple setups. Thanks to the #bobcadafterdark
videos. Time will tell what I got myself into ;)
Pro Engineer wildfire runs on Linux M180 - where to get?
solidworks via EAA - but no Linux so nothing-burger.
Peter Stanton(edge precision) uses ESPRIT what uses for CAM
(over $5k) - CAD - spceclaim http://www.spaceclaim.com
Possible Linux stuff - FreeCAD.
solvespace (limited) - onshape(not free)
3D metal printers
https://www.shapeways.com/
Precision parts to
think about
Misumi miniature
ball slides
Keyless shaft
locking
Misumi KPL300
Ringfedder RfN 8006
Machining Terms /
Terminology
- Face and Flank
- On a cutting edge the face(AKA rake-=surface) is the side
where the chip is formed and the flank is next to the new
surface of what it being cut. There are two flanks on a lathe
cutter - Flank(major) cuts as one feeds in Z - Flank(minor) cuts
as one feeds in X(cross-slide) or plunge cut. The nose
radius is where the two flanks connect.
- Mandrel vs Arbor
- A mandrel holds work, an arbor hold tooling
- Staking
- Punching operation (often with center punch) to deform a part
mostly to capture a part.
- Dutchman
- A hole with pin parallel the shaft at the intersection of a
shaft and hole to prevent rotation.
- Weldon flat
- A ground flat - typically on an endmill that a grub screw
clamps to. See
- Whistle Notch
- A beveled notch that is an improvement on a weldon flat in it
helps resist axial motion. See
- Pawl
- pawl is a movable lever that engages a fixed component to
either prevent movement in one direction or restrain it
altogether. As such, it is a type of latch and can also be
considered a type of dog. It typically consists of a
spring-loaded lever that engages a mating component at a steep
enough angle to restrain it. Pawls are often tapered, being
widened at their pivot for anchoring and narrow at their tip.
- Dog
- a dog is a tool or part of a tool, such as a pawl, that
prevents or imparts movement through physical engagement. Or it
may hold another object in place by blocking it, clamping it, or
otherwise obstructing its movement. A lathe dog transmits rotary
motion from a faceplate to a workpiece mounted between centers
in a lathe.
- Tommy bar or T-bar
- A short rod used as a lever or handle for turning a jackscrew,
socket wrench, or pin spanner wrench by being inserted loosely
in the hole provided for that purpose.
- HSS
- High Speed Steel
- SPFL
- Spiral FluteHSSE
- High Speed Steel with cobalt?
- E11
- ISO 286-2 tolerance class E11
- GH3
- GH3 = Ground High 3 Tolerance class H3
Equipment
Plates and angles
Large Cast iron lapping plate Bush - Milwaukee 18" x 15" ( Grooves
are .078”W(2mm) x .100”D on .531” (13.5mm) centers. )
Lapping plate Challeng machinery grand haven MI 10" x 14"
surface plate Rahn 37230 !4" x 14"
Shars Granite Square - rt angle - 254 mm x 152 mm x 25mm
Surface Plate unnamed 9 x 12
Surface plate unnamed
Granite sink cutout 8.5 x 8
Step right angle 6 x 6
Cylindrical Square 6"
Surfcenter Brunswick Engineering Inc.
Manufactures Data
sheets
Mitutoyo https://www2.mitutoyo.co.jp/eng/support/service/parts_list/index.php
Techniques
Interference fits
0.2mm for a a 140mm bore? approximently 1/1000
Machining glass
- mount on machine wax
- carbide mill or drill
- RPM 1000-2000 RPM - for 4mm end mill or more? - Will wear
tool.
- Use cutting fluid to prevent fracture cooling.
- depth of cut - 200um
People
Phil Perry Hepler KS 66746 - restores machines.
Peter L Stanton - edge precision - Huston TX
Lance Baltzley - source of precision ground stones.
Chris Baca and Mikey Baca - Precision Instrument Repair 909 766
5041 or 760 561 2400
Email